1-203-200-0302
sales@apextoolworks.com
Mon-Sat 9AM - 6PM EST
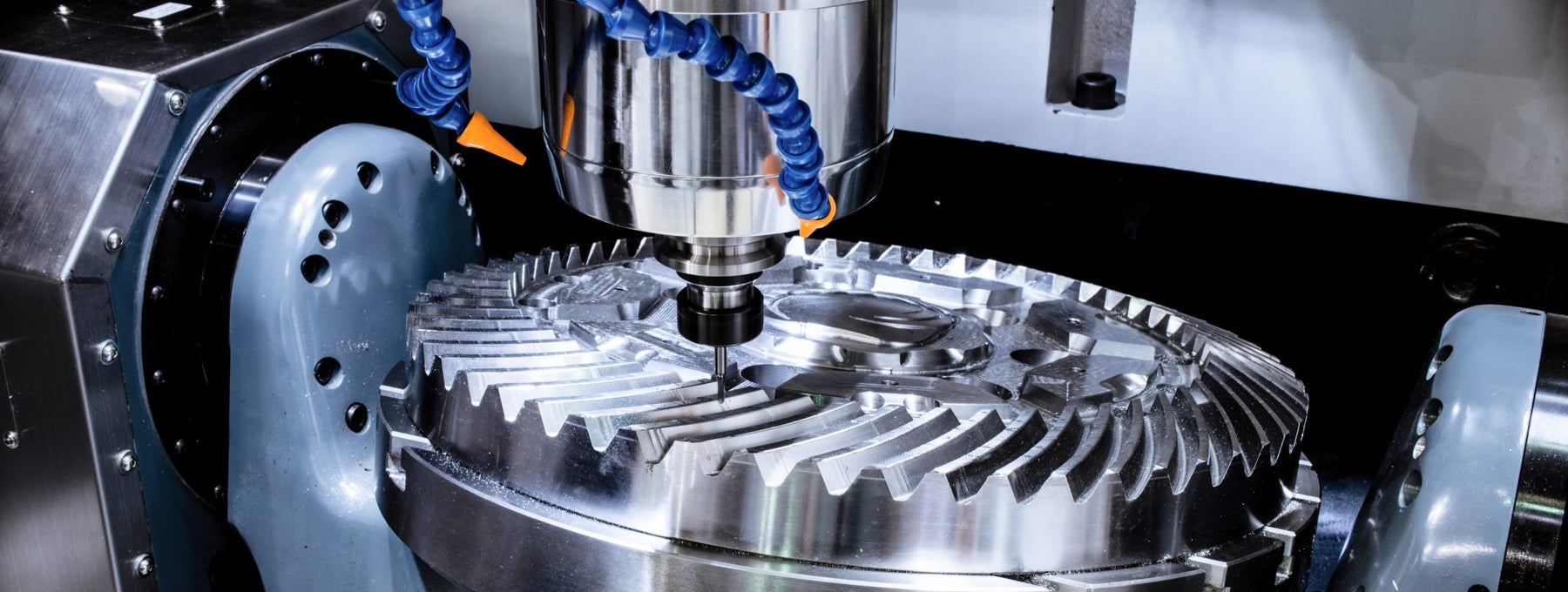
Mastering Metalworking with CNC Milling Machines
CNC milling machines have transformed metalworking by offering precision, efficiency, and flexibility. Whether you’re new to CNC or an experienced machinist upgrading your equipment, understanding these machines’ fundamentals is crucial. This guide explores the essentials of CNC milling, delves into machine types, and offers tips on choosing and maintaining the right machine.
What is CNC Milling?
CNC milling, or Computer Numerical Control milling, automates the machining process using programmed instructions to guide cutting tools. It excels in producing intricate parts with tight tolerances. Unlike manual milling, CNC machines deliver consistency and speed, making them invaluable in industries like aerospace, automotive, and medical manufacturing.
With the ability to cut various metals—including aluminum, steel, and titanium—CNC milling offers unmatched versatility. Its automation reduces human error and increases output efficiency, making it a cornerstone of modern manufacturing.
Understanding CNC Milling Machines
CNC milling machines consist of several key components that determine their functionality. The spindle powers the cutting tools and adjusts speed and torque for different materials. An advanced tool changer allows the machine to switch tools seamlessly for multi-step processes. The control panel acts as the brain, interpreting CAD files and guiding operations with precision. Stability, provided by a durable worktable, is vital to maintaining accuracy, especially during high-speed machining.
Choosing the Right CNC Milling Machine
Choosing the right CNC milling machine involves balancing your project requirements, budget, and operational needs. Here’s a detailed breakdown of common types, their applications, and their costs:
Type | Application | Key Features |
3-Axis CNC |
General-purpose machining | Slotting, simple contours |
4-Axis CNC | Complex parts with multiple faces | Added rotary axis |
5-Axis CNC | Aerospace, medical devices, tight tolerances | Cutting from all angles |
Mini CNC | Hobbyists, prototyping | Compact and lightweight |
Vertical Milling Machine | Precise vertical cuts | Vertically aligned spindle |
Horizontal Milling Machine | Heavy-duty, deeper cuts | Horizontally aligned spindle |
3-axis machines are a cost-effective choice for basic operations, while 5-axis machines handle intricate geometries like turbine blades. Mini CNCs are excellent for hobbyists or small-scale work, whereas horizontal milling machines excel in heavy-duty, deep cuts for industrial applications.
Maintenance and Troubleshooting
Regular maintenance ensures your CNC machine stays in optimal condition. Daily tasks like cleaning chips, lubricating parts, and checking tool alignment are essential. Calibration is another critical aspect; even slight misalignments can affect precision.
Troubleshooting common issues like overheating or software glitches is easier with diagnostic tools included in modern machines. Keeping software updated and replacing worn tools promptly can prevent major breakdowns.
Always check with your manufacturer for the recommended maintenance schedule, but here are a few tips to get you started:
Daily Maintenance:
- Verify lubrication levels and top off as necessary.
- Apply grease to any dry or exposed parts.
- Check coolant concentration and ensure fill levels are adequate.
- Empty the chip hopper.
- Inspect hydraulic system levels.
- Wipe down surfaces to prevent the accumulation of small metal shavings.
Monthly Maintenance:
- Clean or replace air filters.
- Inspect and clean coolant filters.
- Clean radiators and cooling fans.
- Review oil fill records for signs of abnormal oil consumption.
- Remove and thoroughly clean the chuck and jaws.
- Grease and adjust chains or conveyors as needed.
Yearly Maintenance:
- Fully drain and clean the coolant tank, removing metal chips missed by the conveyor, checking for bacterial growth, and inspecting the system.
- Test hydraulic oil for contaminants and replace filters.
- Drain and clean the lubrication unit, replacing the oil.
- Inspect the headstock for tapering.
- Test drawbar tension.
- Examine the chuck cylinder for wear or damage.
- Run a backlash program and replace the X and Y-axis gibs if necessary.
How long do CNC machines usually last with proper maintenance? Trusted performance can be expected for as long as 20 years. Again, these are rugged machines built to withstand harsh environments and continuous use.